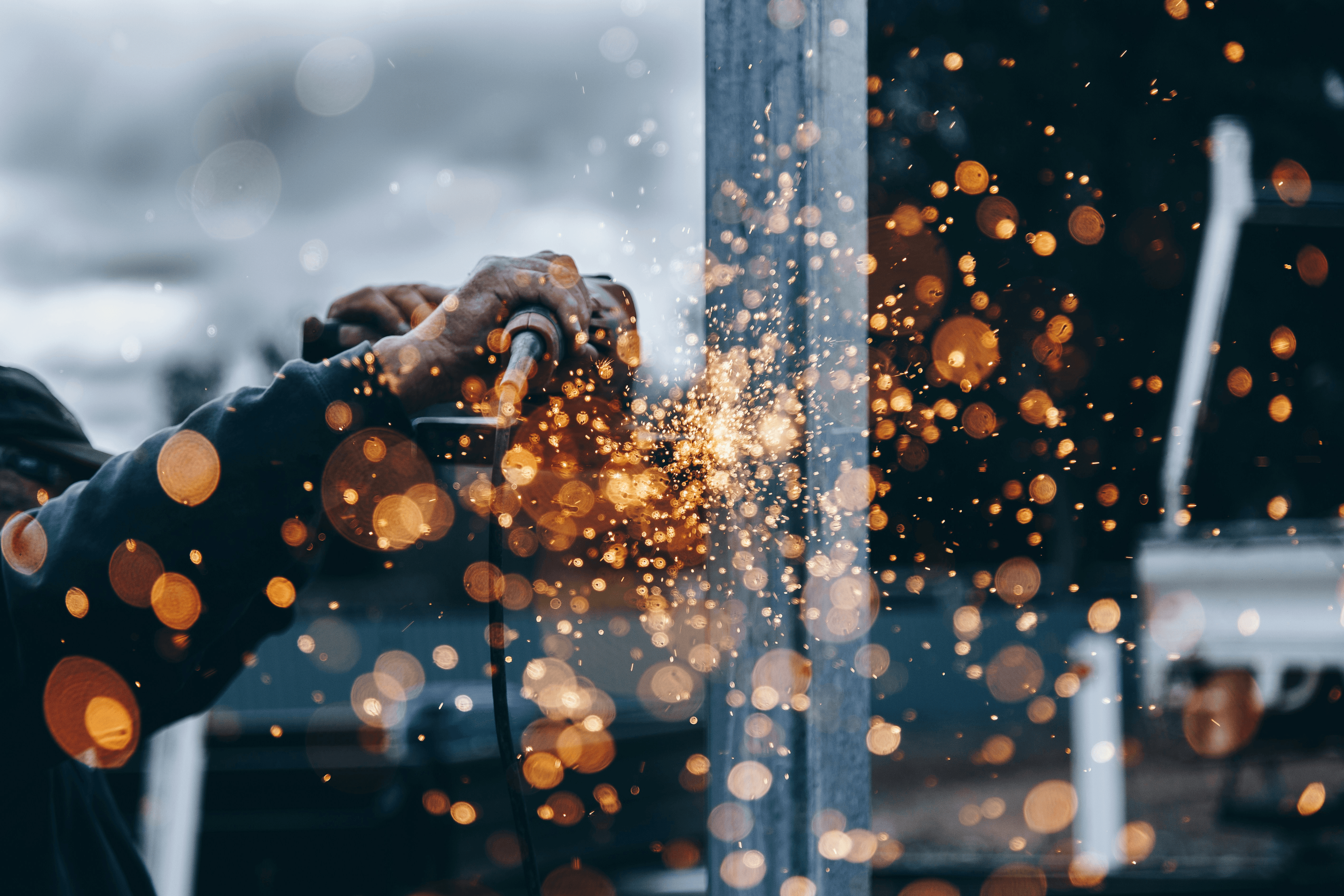
Our Capabilities
A comprehensive suite of in-house capabilities, ensuring quality control and innovation at every stage of the manufacturing process
Our End-to-End Process
From concept to delivery, our integrated approach ensures quality and precision at every step
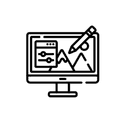
Design
Starting with concept development and detailed engineering design
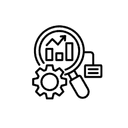
Analyze
Validating through FEA and simulations for optimal performance
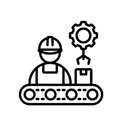
Manufacture
Casting, Forging, Precision Machining and fabrication to exact specifications
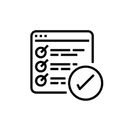
Test
Rigorous testing under simulated and actual operating conditions
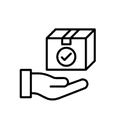
Deliver
On-time delivery with comprehensive documentation
Our Core Capabilities
Discover our comprehensive range of in-house manufacturing capabilities that ensure complete quality control throughout the production process
Design & Development
From concept to prototype, we bring your ideas to life with precision and innovation.
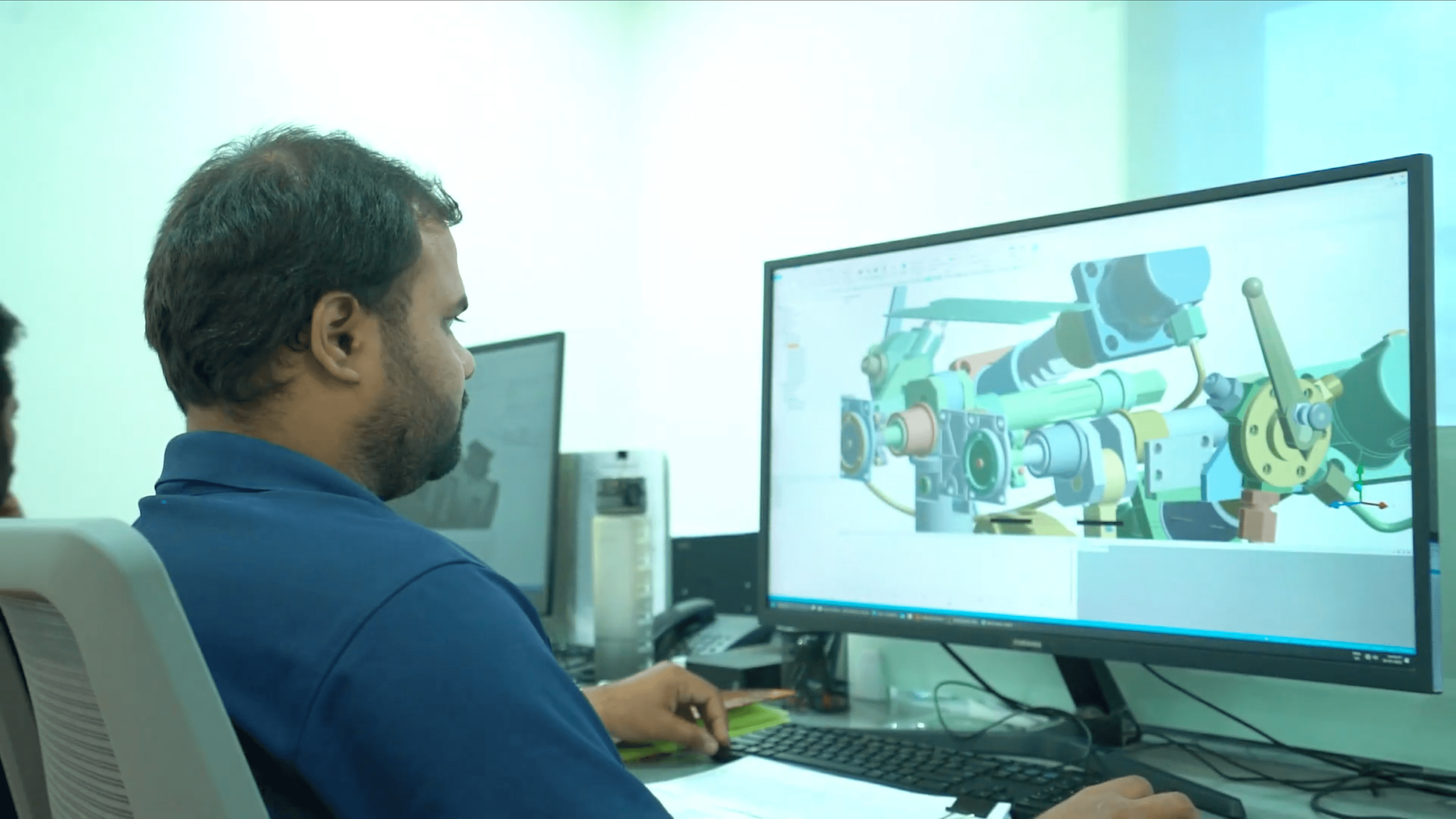
- Concept Design & Engineering
- 3D Modeling & Analysis
- Finite Element Analysis (FEA)
Precision Machining & Fabrication
Achieving micron-level accuracy on complex geometries with advanced multi-axis machining.
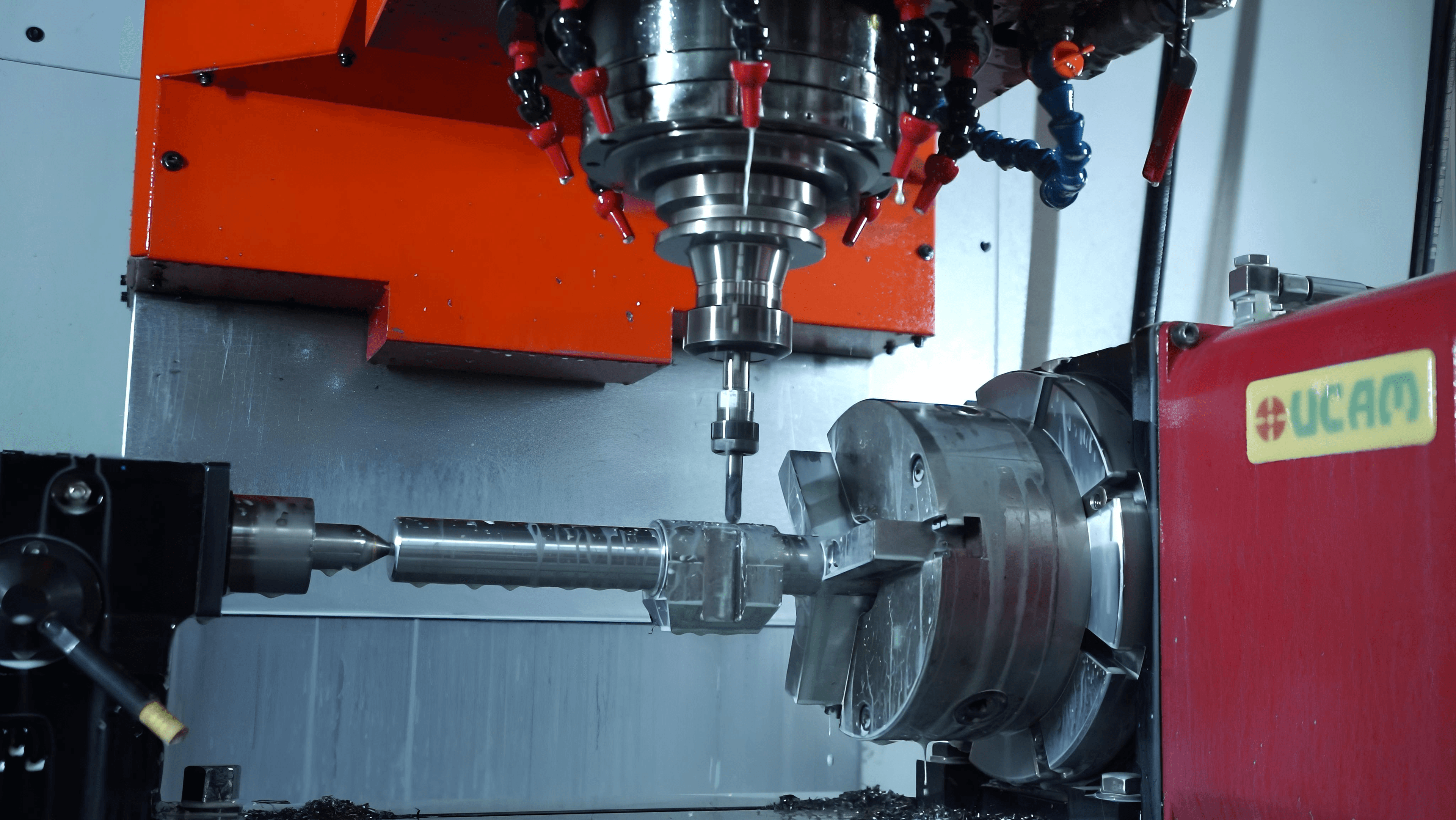
- Expertise with Titanium, NAB, Inconel, Maraging Steels & Special Alloys
- Single setting 3, 4, and 5 axis machining
- Tolerances up to 2 microns
Specialized TIG Welding
Certified and specialized welding in clean environments for critical materials and applications.
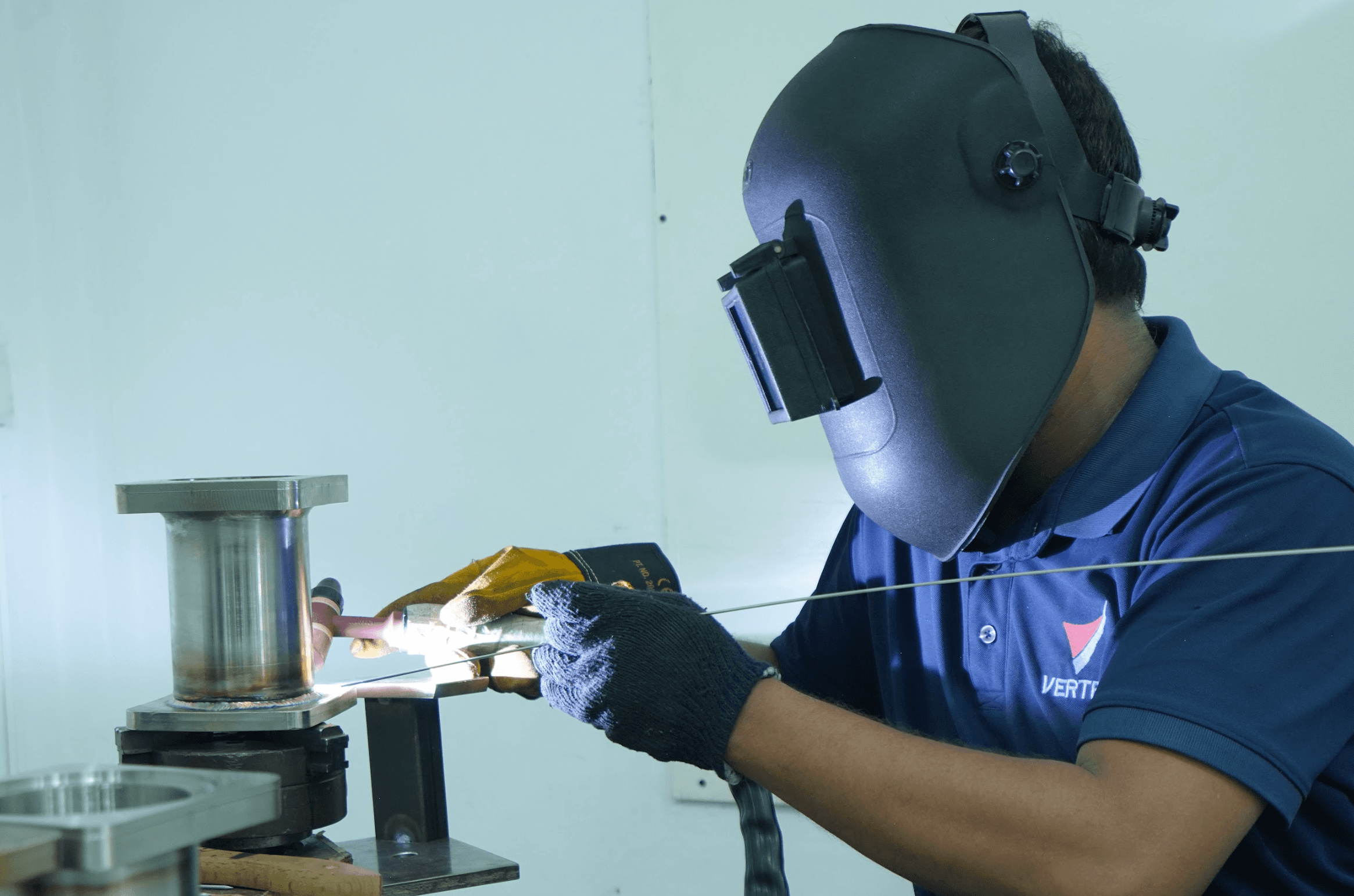
- Titanium welding in Argon purged environment
- Expertise with Copper Alloys, Stainless Steels & Inconel
- 6G Certified Welders for Nuclear Grade Welds
Casting
In-house foundry producing reliable, high-quality castings for various applications.
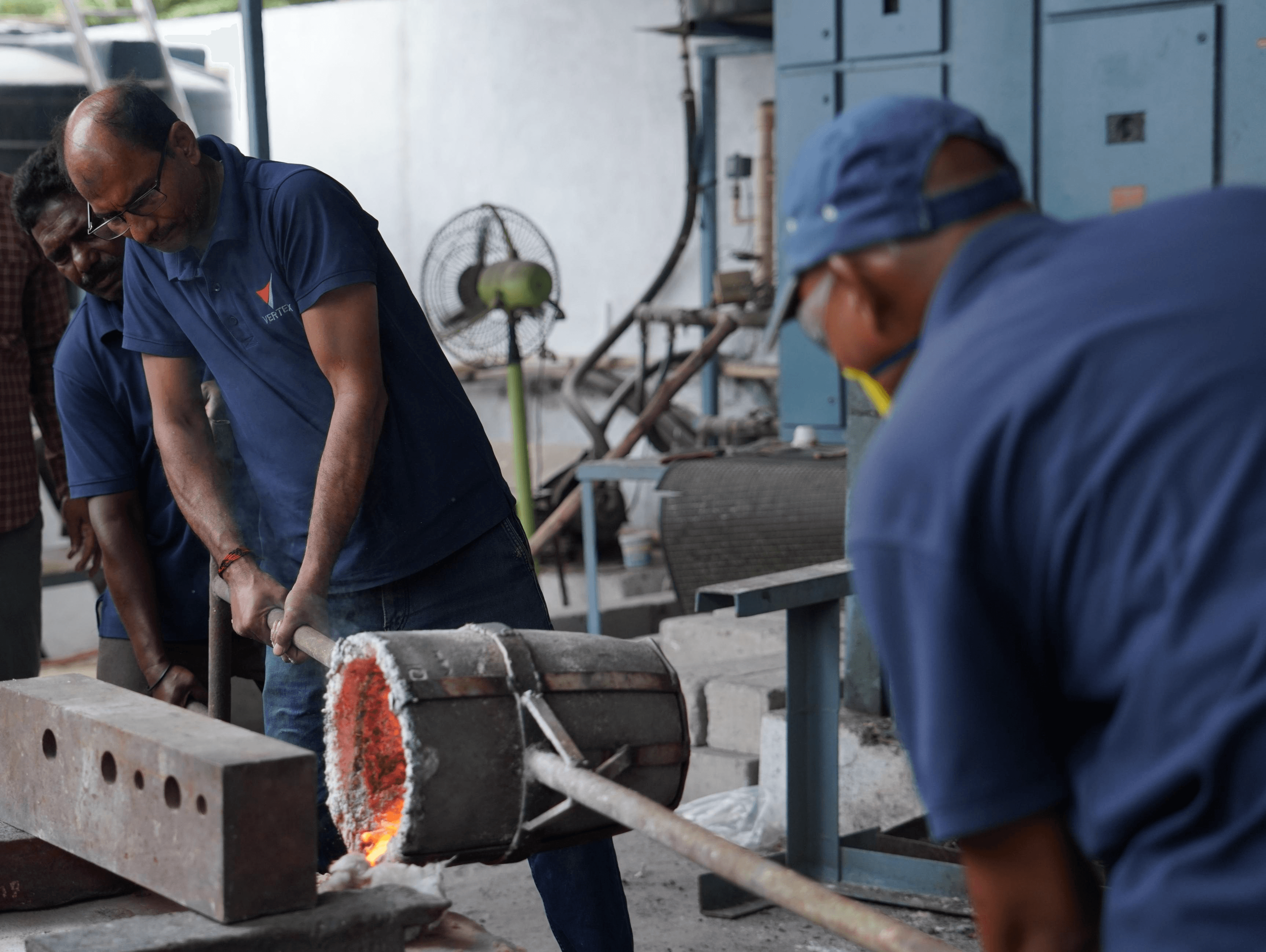
- Materials: Copper Alloys, Alloy Steels & Stainless Steels
- Sand Casting: 1kg to 100kg (up to 1.3 tons with partners)
- Investment Casting: 50g to 35kg
Forging
Expertise in hot forging for components requiring high material integrity under stress.
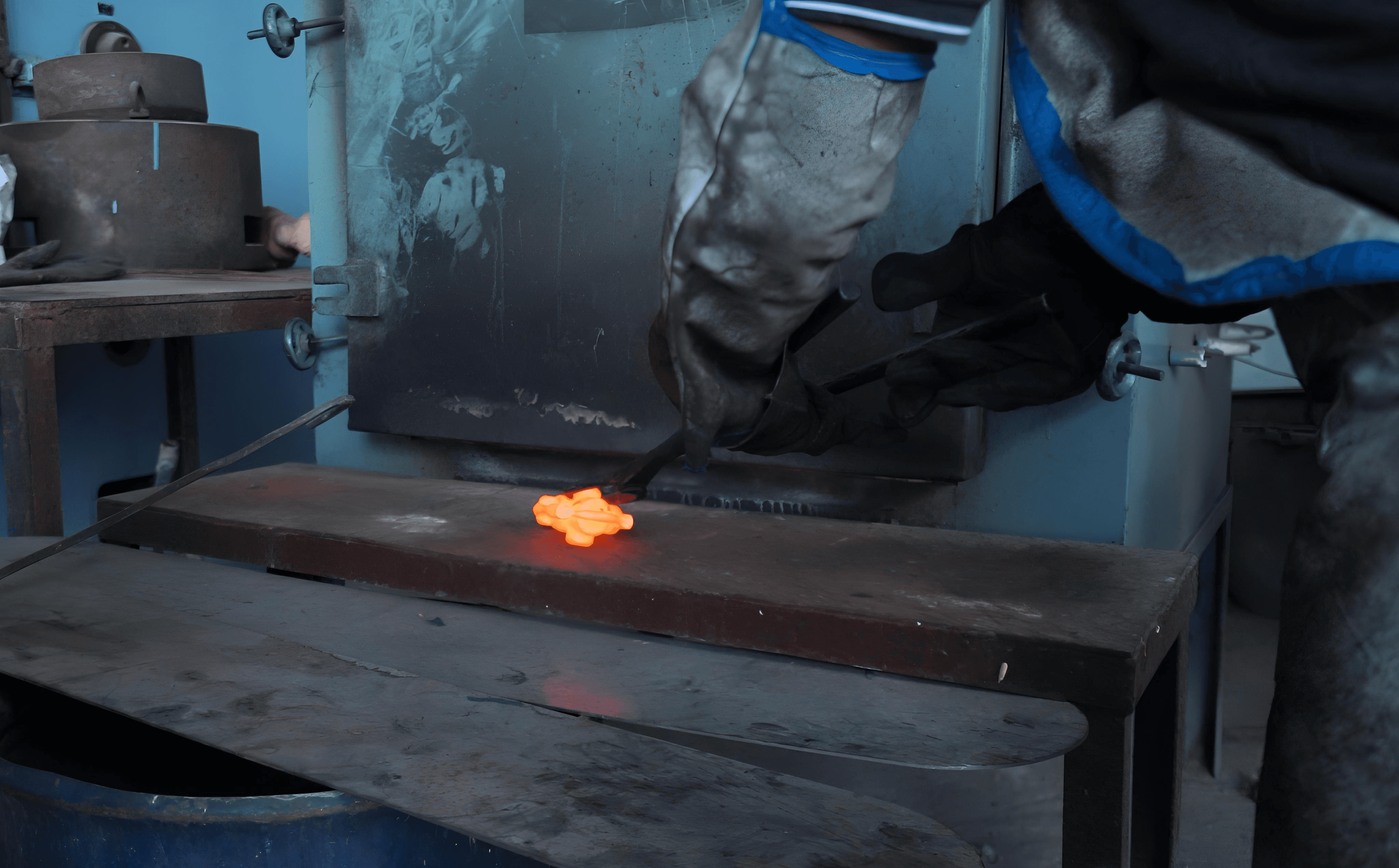
- Materials: Titanium, Alloy Steels, Stainless Steels & Copper Alloys
- Applications for high-stress, high-pressure (up to 600 Bar)
- Maximum 300mm Diameter
Assembly & Cleanroom Operations
Dedicated facilities for assembling sensitive and complex components with precision.

- 10,000 Class Cleanroom (1500 sq ft)
- Custom assembly fixtures and tools
- Precision and repeatability in assembly processes
Heat Treatment & Surface Treatment
In-house capabilities to enhance material properties and component finishes.
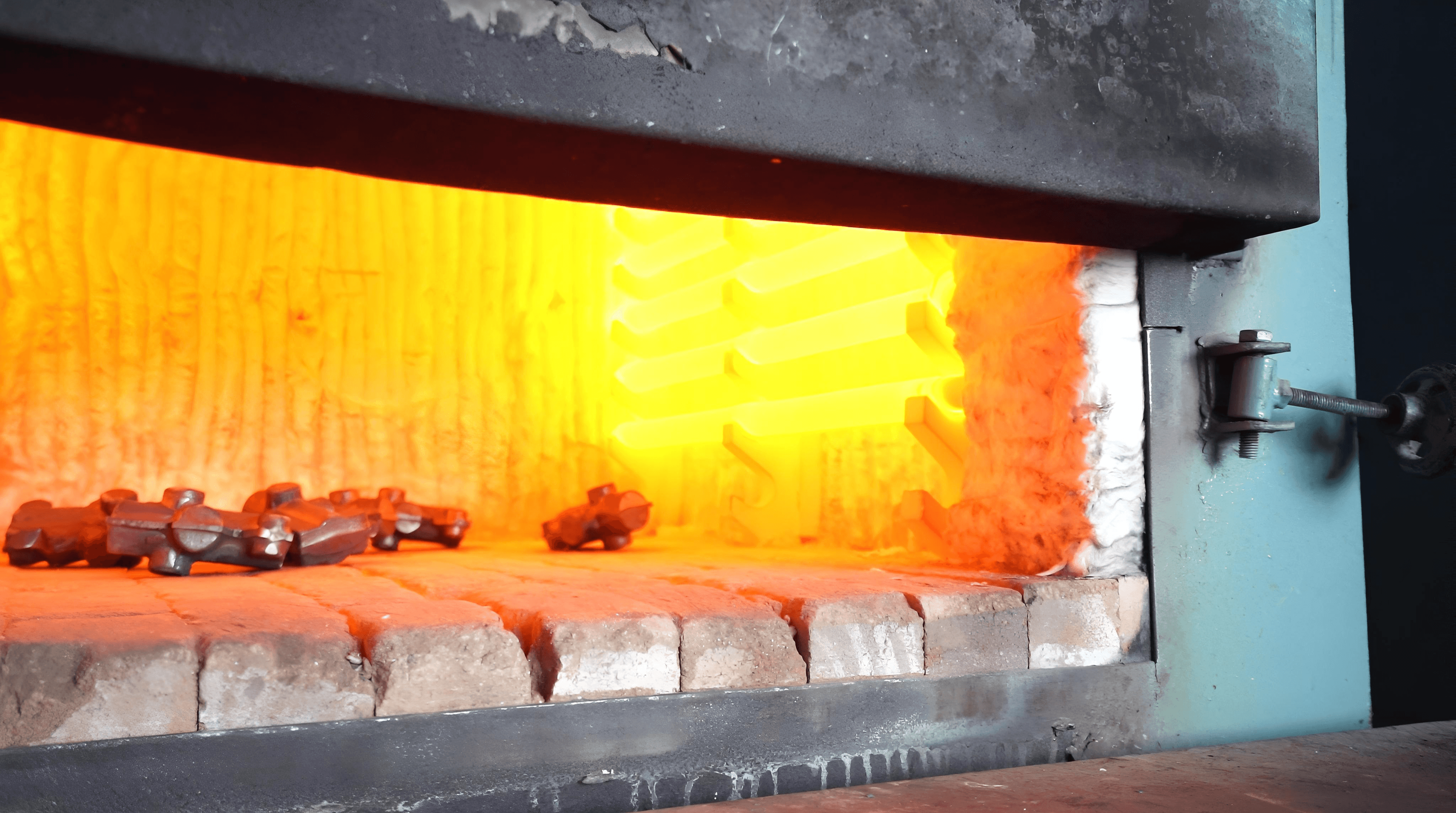
- Comprehensive Heat Treatment processes
- Anodizing (including Titanium)
- Quenching & Tempering
Testing & Quality Assurance
Rigorous testing procedures to validate performance and reliability under demanding conditions.
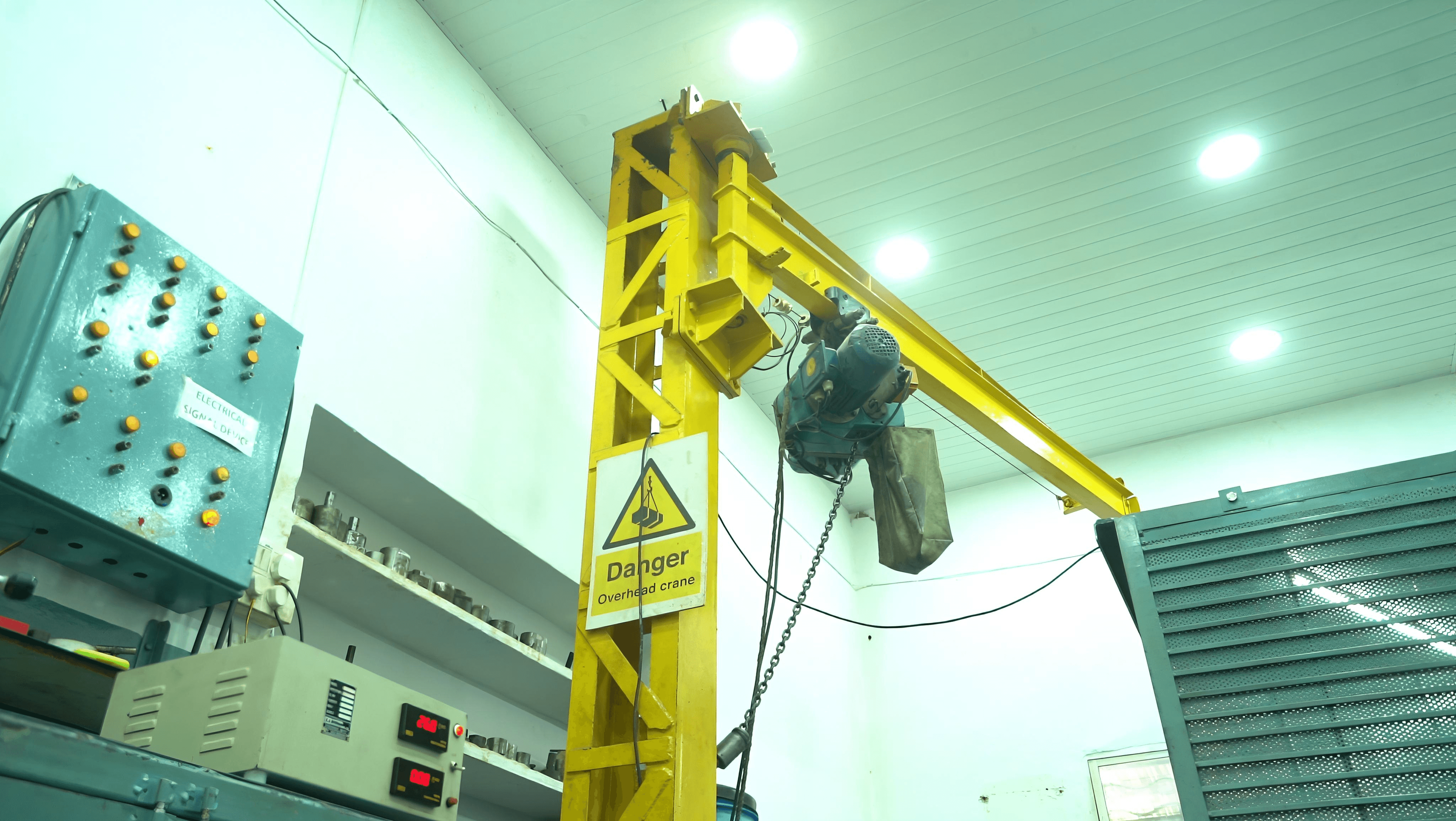
- Non-Destructive Testing (NDT) & Dye Penetrant Testing (DPT)
- High-Pressure Pneumatic (400 Bar), Hydraulic (1000 Bar) & Hydraulic Cyclic (500 Bar) Testing
- Specialized tests: CV & Fuel Injection
Value Added Services
Extending our support beyond manufacturing through the entire product lifecycle.
- Installation, STW & commissioning expertise
- Post-delivery support
- On-time delivery of customized products
Quality Certifications
Our capabilities are backed by international quality certifications and standards
ISO 9001:2016
Quality Management System
AS9100D
Aerospace Quality Management